Are you planning to create a unique epoxy table that combines the beauty of solid wood with crystal-clear resin?
With LuminaCast 9 Ocean Flow epoxy resin, which meets food contact certification (1935/2004 ES), you will not only achieve a stunning design but also a safe and durable surface that can be used in kitchens and dining areas. This low-viscosity professional resin is perfect for casting tables, countertops, serving trays, and other furniture where high mechanical strength and long-term durability are essential.
To help you succeed, we have prepared a detailed guide that walks you through the entire epoxy table-making process– from choosing the right wood, preparing it, pouring the resin, to final finishing and surface treatment. With LuminaCast 9 Ocean Flow and our guide, you will achieve professional results, whether you are an experienced craftsman or a beginner.
✅ Why choose LuminaCast 9 Ocean Flow for your epoxy table?
✔ Certified for food contact – perfect for kitchen countertops and dining tables
✔ High clarity and UV stability – resistance to yellowing and long-lasting durability
✔ Self-degassing formula – minimizes bubble formation during pouring
✔ Low viscosity – ideal for wood encapsulation and deep casting
Let’s dive into the complete step-by-step process of making an epoxy resin table that will add unique style and elegance to your interior.
LuminaCast 9 Ocean Flow
- Certification 1935/2004 ES
- Mixing ratio 2:1 by weight
- Casting height up to 10 cm and working time up to 240 minutes
- Optimized for table casting, lamp making, or jewelry production, where a greater casting height is required
- Creates an exceptionally smooth and glossy surface
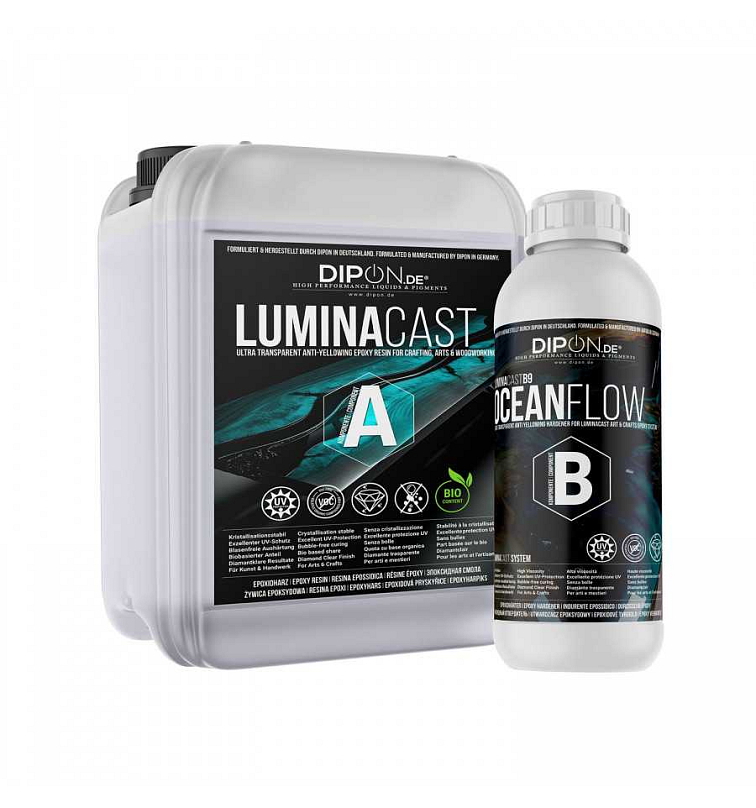
How to Choose and Prepare Wood for an Epoxy Resin Table
Choosing the right wood is a crucial step in creating an epoxy resin table, as it directly impacts both the aesthetics and durability of the final product. Combining wood with epoxy resin requires careful preparation to ensure a strong bond, prevent defects, and achieve long-lasting results.
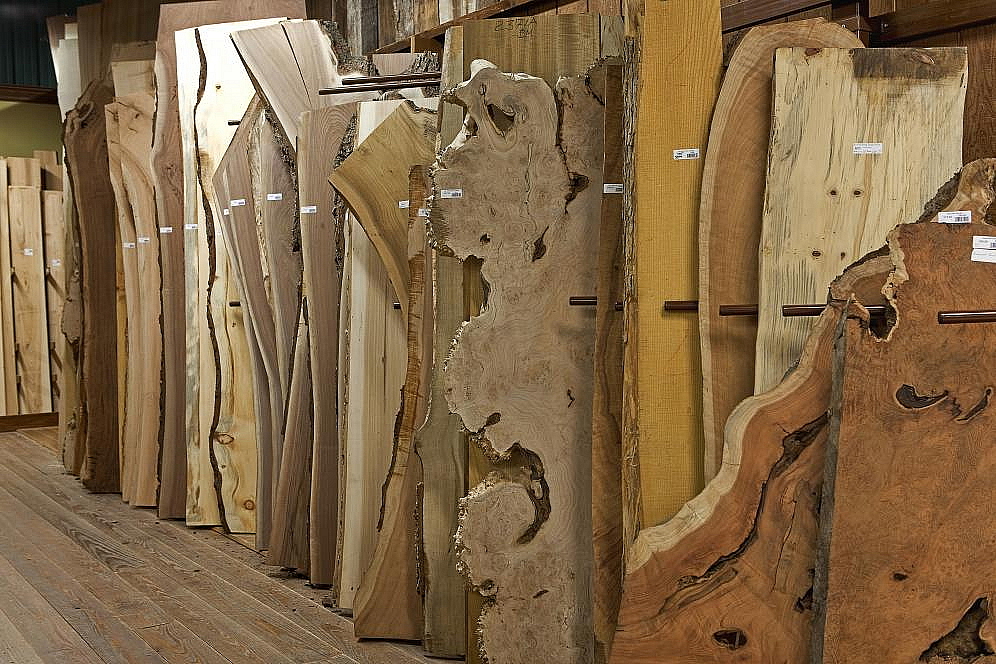
1️⃣ What Type of Wood to Choose?
When selecting wood for an epoxy table, look for a piece with unique grain patterns, natural edges (live edge), and interesting shapes to add a distinctive character to your furniture. Wood with cracks and knots can also be used creatively by filling them with epoxy resin.
Recommended types of wood:
✔ Oak – durable, strong, and has a rich texture
✔ Walnut – darker tones with a sophisticated grain
✔ Ash – light-colored, flexible, and easy to work with
✔ Exotic woods (e.g., teak, acacia) – naturally moisture-resistant
2️⃣ Why is Wood Moisture Content Important?
Unseasoned wood can crack, warp, or cause epoxy resin delamination, leading to project failure. To avoid this, always use properly dried wood with a moisture content below 12%, ideally under 10%.
🔹 How to measure wood moisture?
A moisture meter is a handy tool to determine whether your wood is ready for use. There are both hobby-grade and professional moisture meters – we recommend at least a basic model for accurate readings.
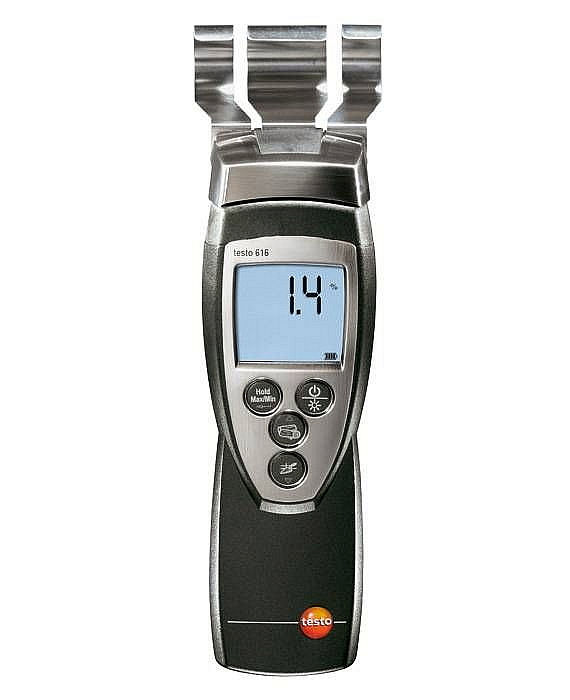

3️⃣ Preparing Wood for Epoxy Pouring
Before pouring epoxy resin, make sure the wood is properly prepared:
✔ Sanding the surface – removes dirt, grease, and uneven textures
✔ Sealing with a thin epoxy layer – prevents air bubbles, especially in porous woods
✔ Filling cracks and knots – pre-sealing imperfections before the main pour helps avoid defects
Summary – Key Points When Choosing Wood for an Epoxy Table
✅ High-quality solid wood with distinctive grain for a premium look
✅ Low moisture content (below 10-12%) to prevent warping and cracking
✅ Proper surface preparation, sealing, and finishing for a perfect result
Wood Penetration for an Epoxy Resin Table – A Key Step for a Perfect Finish
Before pouring epoxy resin, proper wood penetration is essential to prevent air bubbles and improve adhesion between the resin and the surface. Wood is a porous material, and tiny air pockets trapped inside can release air during curing, causing unwanted bubbles and defects in the final casting.
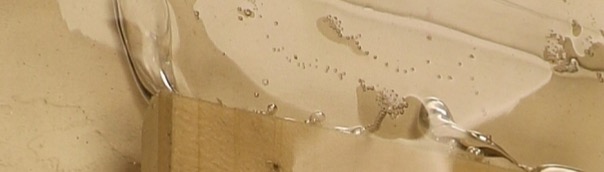
1️⃣ Preparing the Wood Before Penetration
Before applying the penetration coat, make sure the wood is properly cleaned and prepared:
✔ Cut to desired dimensions – adjust the wood to the final size of the table
✔ Remove bark and loose parts – eliminate any unwanted debris that could affect surface smoothness
✔ Clean off dust and sawdust – use a brush, air blower, or cloth to remove fine particles
✔ Ensure the surface is dry – moisture can interfere with the resin reaction
2️⃣ How Does Wood Penetration Work?
Wood penetration involves applying a thin layer of epoxy resin, which seals the wood pores and prevents air from escaping during the curing process. There are two main penetration methods:
🔹 Using Casting Epoxy Resin
✔ Apply the same resin that will be used for the main pour
✔ Spread a thin layer using a brush or roller
✔ Allow to dry until slightly tacky (approx. 4–6 hours) before pouring the main layer
Drawback: Longer curing time and requires precise application
🔹 Using Fast-Penetrating Epoxy Resin
✔ Special low-viscosity laminating resin
✔ Rapidly penetrates deep into the wood, sealing and reinforcing the surface
✔ Shorter curing time (usually 1–3 hours)
Drawback: Requires a compatible penetration resin with the main epoxy
Penetrated Wood ✅
- Minimizes air bubbles
- Improves resin adhesion
- Prevents excessive resin absorption
- Strengthens wood structure
- Results in a smoother, more precise final surface
Non-Penetrated Wood ❌
- High risk of air escaping into the resin
- Weaker bond, possible delamination
- Uneven absorption, potential discoloration
- Increased risk of cracks and defects
- Uneven finish, possible imperfections
4️⃣ Tips for a Perfect Penetration Process
✔ Apply epoxy evenly – ensure full coverage for a uniform seal
✔ Use a high-quality brush or roller – for smooth application without streaks
✔ Let it dry until tacky, not fully cured – a tacky surface improves bonding with the next layer
✔ Focus on edges and cracks – these areas are most prone to air leaks
Summary – Why is Wood Penetration Important?
🔹 Prevents bubble formation in epoxy resin
🔹 Enhances resin adhesion to the wood surface
🔹 Ensures even resin absorption and avoids staining
🔹 Protects wood from excessive resin penetration and deformation
💡 Want a flawless epoxy resin table without bubbles? Don’t skip proper wood penetration – a small step that makes a huge difference in the final result! 🚀
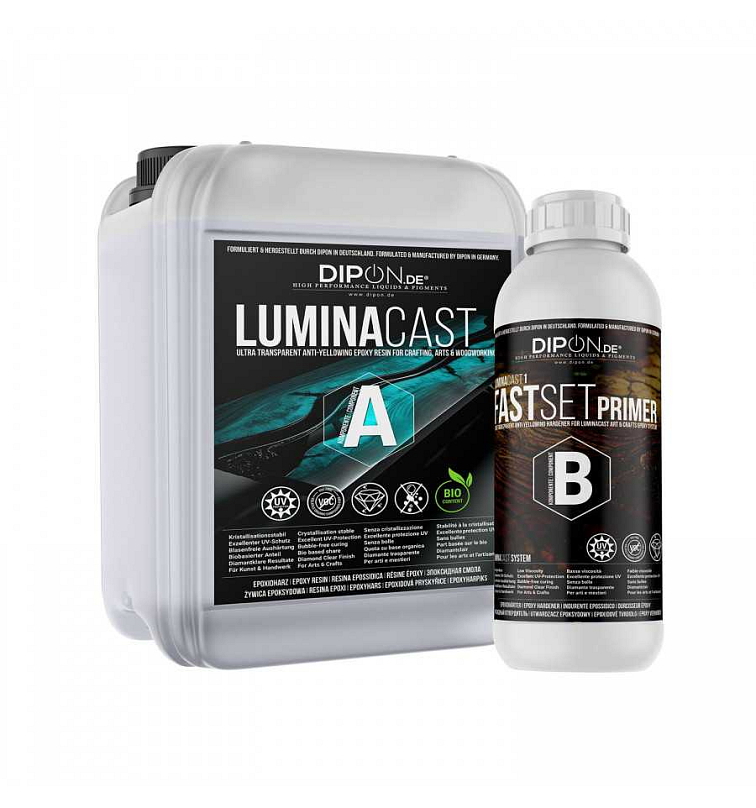
LuminaCast 1 Fast Set Primer
- Highly effective penetration – specially designed for sealing wood and other porous surfaces
- Deep sealing action – penetrates deep into fibers and porous materials, ensuring perfect preparation before epoxy resin casting
- Fast processing time – at room temperature, the primer can be overcoated with epoxy within 60–120 minutes
- Minimizes air bubbles – effectively seals pores and reduces the risk of air escaping into the epoxy resin, resulting in a perfectly smooth finish
- Compatible with casting epoxies – ideal as a base layer for deep pours, tabletops, artistic projects, and laminating applications
- Enhanced epoxy adhesion – creates a strong bond between the substrate and the epoxy resin, ensuring long-lasting durability of the final project
How to Make a Mold for Epoxy Resin Casting – A Step-by-Step Guide
Creating a high-quality mold is crucial for achieving a perfect shape, smooth surface, and easy demolding when making an epoxy resin table. Choosing the right material and technique affects not only the final look of your project but also simplifies the process and minimizes the risk of resin adhesion to the mold.
1️⃣ What Material to Use for an Epoxy Resin Mold?
Several materials can be used for making epoxy resin molds, each with its own advantages and disadvantages:
- Polypropylene (PP): Non-stick surface, reusable, smooth finish
- Requires precise cutting and assembly
- MDF boards and plywood: Affordable, easy to shape
- Resin adheres to the surface, needs separation tape or coating
- Silicone mold: Ideal for smaller castings, flexible
- Expensive, requires a special mold-making process
The most commonly used materials for epoxy table molds are polypropylene (PP) or MDF boards treated with separation tape.
2️⃣ Polypropylene Mold – The Best Solution for Epoxy Casting
🔹 Polypropylene (PP) is one of the best materials for making epoxy resin molds because:
✔ Epoxy does not stick to it, so no release agent is needed
✔ Reusable – an economical solution for frequent casting
✔ High mechanical resistance – does not absorb resin, does not warp, and is easy to clean
✔ Ideal for larger molds – excellent for epoxy tables
🔹 Pro Tip for Working with Polypropylene:
✔ PP thickness should be at least 2 mm for the bottom and 4 mm for side walls to ensure strength
3️⃣ MDF or Plywood Mold – Alternative with Polypropylene Separation Tape
If polypropylene is not available, an MDF board or plywood mold can be used, but it must be treated with a separation layer to prevent the resin from sticking.
🔹 How to do it?
✔ Use polypropylene separation tape – ensures easy demolding of the epoxy table
✔ Apply tape to both the bottom and side walls of the mold – overlap each strip by at least 3 mm
✔ Seal the mold corners with silicone – prevents resin leakage
Advantages of Using Separation Tape
- Easy to apply to different mold types
- Quick and cost-effective method for single-use molds
- Provides a smooth epoxy casting surface
Disadvantages of Using Separation Tape
- Single-use application – the tape must be replaced for each use
- If not applied properly, epoxy may seep underneath
4️⃣ Key Steps for Making an Epoxy Resin Mold
✔ Choose the right material – ideally polypropylene or MDF with separation treatment
✔ Properly seal the mold joints – use silicone or adhesive to prevent epoxy leakage
✔ Use a high-quality release agent – necessary for MDF molds with separation tape
✔ Ensure a smooth mold surface – for a flawless epoxy resin finish
💡 Want to create a perfect epoxy resin table? A well-made mold will simplify the process, minimize errors, and ensure a professional result! 🚀
Mixing and Pouring Epoxy Resin
When working with epoxy resin LuminaCast 9 Ocean Flow, it is crucial to follow the correct mixing, temperature conditions, and pouring process to achieve a perfect, bubble-free, and smooth casting.
1️⃣ Ideal Temperature for Mixing and Pouring Epoxy Resin
The temperature of the environment in which epoxy resin is mixed and poured affects curing speed, casting quality, and the formation of unwanted bubbles.
✔ Recommended temperature for LuminaCast 9 Ocean Flow: 15–25 °C (59–77 °F)
✔ Maintain a stable temperature in the room throughout the curing process
✔ Avoid extreme temperatures – low temperatures slow down curing, while high temperatures can cause exothermic reactions, cracking, and yellowing
💡 Tip: If the resin is too cold, heat it to 25–30 °C (77–86 °F) in a warm water bath (do not exceed 40 °C/104 °F) to reduce its viscosity and improve mixing.
2️⃣ Proper Mixing of Components A and B
🔹 Mixing ratio for LuminaCast 9 Ocean Flow: 2:1 by weight
🔹 Maximum measurement tolerance: ±1% (use an accurate scale)
🔹 Use a clean plastic or silicone mixing container – avoid glass or paper cups
Mixing procedure:
✔ Pour the measured amount of component A into a container
✔ Add component B in the correct ratio (2:1 by weight)
✔ Stir for at least 3–4 minutes (for larger volumes, up to 5 minutes)
✔ Ensure thorough mixing, including the sides and bottom of the container
✔ After the first mixing, transfer the mixture into a new container and mix again for 2–3 minutes
💡 Why is double mixing important?
During the first mixing, unmixed resin and hardener may remain on the sides and bottom, leading to improper curing and sticky spots in the final casting.
3️⃣ How to Pour Epoxy Resin Correctly?
🔹 Pouring epoxy resin correctly is essential to minimize bubbles and achieve a flawless result.
Key steps for pouring epoxy resin:
- Pour slowly and from a low height to minimize air entrapment
- Avoid rapid pouring, which can introduce bubbles
- Optimal pouring thickness for LuminaCast 9 Ocean Flow:up to 10 cm (4 inches) in one pour
- For thicker layers, pour in stages – wait 24–36 hours between pours
💡 Tip: After pouring, let the resin sit for 15–25 minutes to allow air bubbles to escape naturally.
4️⃣ How to Eliminate Air Bubbles?
Bubbles can form during mixing or pouring of the resin. Removing them is crucial for a flawless finish.
✔ Use a vacuum chamber – the best method for removing bubbles before pouring
✔ Preheat the resin before pouring – reduces viscosity for better air release
✔ Use a heat gun or torch – gently pass over the surface to pop bubbles
✔ Epoxy AB Corrector Spray – a specialized spray designed to eliminate bubbles on the surface
💡 Avoid excessive heating! Overheating can cause yellowing, overheating, and resin deformation.
5️⃣ Layering Epoxy Resin – How to Ensure Perfect Bonding?
If you need to pour epoxy resin in multiple layers, follow these steps:
✔ Pour the next layer at the right moment – when the previous layer is not fully cured but is no longer sticky to the touch
✔ If the previous layer has fully cured, sand it lightly with P100 grit sandpaper – improves adhesion between layers
✔ Allow sufficient curing time between layers (24–36 hours depending on conditions)
💡 Why is layering timing important?
If you pour the next layer too late, a visible transition may form between layers, affecting the final look.
Summary – How to Properly Mix and Pour Epoxy Resin LuminaCast 9 Ocean Flow?
🔹 Maintain ideal temperature conditions – 15–25 °C (59–77 °F)
🔹 Follow the correct mixing ratio – 2:1 by weight
🔹 Mix slowly and thoroughly, transfer to a clean container, and mix again
🔹 Pour slowly and in stages to minimize bubbles
🔹 Use a vacuum chamber, heat gun, or anti-bubble spray
🔹 When layering, ensure the correct timing for the next pour
💡 Want to achieve a perfect epoxy casting? Follow the correct procedures and use high-quality epoxy resin LuminaCast 9 Ocean Flow, which offers excellent UV stability, high clarity, and food-safe certification! 🚀
Calculation of the amount of epoxy resin
📌 Calculator for determining total resin quantity:
✅ Enter length × width × height (in cm or meters)
✅ The calculator converts volume to liters or kilograms based on resin density
📌 Calculator for calculating components A and B based on mixing ratio:
✅ Enter total weight or volume of resin
✅ The calculator determines the exact amount of components A and B
Coloring Epoxy Resin: How to Achieve the Perfect Tint?
Epoxy resin is an excellent choice for creative projects because it allows easy coloring and pigmentation. With a wide range of available pigment solutions, powders, pastes, and inks, you can achieve transparent, metallic, or opaque effects. In this article, we will guide you on how to choose the right pigments for your project and how to dose them correctly for the best results.
1️⃣ What Types of Pigments Can Be Used for Epoxy Resin?
When choosing a pigment, it depends on the desired effect – do you want a transparent or opaque look? Should the color be subtle, rich, or metallic?
✅ Pigment solutions – ideal for transparent and translucent effects
✅ Pigment pastes – create vibrant and opaque colors
✅ Metallic pigments – provide a pearl and shimmer effect
✅ Alcohol inks – achieve subtle color transitions and abstract designs
2️⃣ Pigment Solutions: Why and How to Use Them?
2.1 What Are Pigment Solutions?
Pigment solutions are liquid dyes that mix easily with epoxy resin and create transparent and semi-transparent effects. They are ideal for:
✔ Casting into molds and tabletops
✔ Creating a depth effect in resin
✔ Mixing custom color shades
2.2 How to Dose Pigment Solutions Correctly?
✔ Start with a small amount and gradually add more until you reach the desired shade
✔ Typical dosage: 1–3% of the resin’s weight
✔ Mix thoroughly to ensure even color distribution
💡 Tip: For a metallic or iridescent effect, combine pigment solutions with metallic powders.
3️⃣ Metallic Pigments: How to Create Unique Effects?
3.1 What Are Metallic Pigments and Why Use Them?
Metallic pigments are finely ground powders with a pearlescent effect that give epoxy resin a luxurious appearance and depth. They are perfect for making tables, artistic decorations, jewelry, and designer castings.
💡 Choosing pigments with the right particle size ensures even color dispersion in the resin. For the best results, we recommend high-quality pigments from Eye Candy Pigments, widely used by professionals and hobbyists alike.
3.2 Dosing Metallic Pigments
✔ Transparent effect → 0.5 g of pigment per 1 kg/l of resin
✔ Rich color → 1 g of pigment per 1 kg/l of resin
✔ Intense metallic effect → add pigment gradually as needed
There is no universal formula – we recommend starting with a smaller amount and gradually adding pigment until you achieve the desired effect.
4️⃣ Pigment Pastes: How to Achieve Intense Colors?
4.1 Why Use Pigment Pastes?
Pigment pastes are designed for opaque and vibrant coloring of epoxy resin. Their high concentration means only a small amount is needed to reach the desired intensity.
📌 Benefits of Pigment Pastes:
✅ Create solid, fully opaque colors
✅ Can be mixed to create custom shades
✅ Easy to dose and distribute evenly in the resin
💡 Eye Candy Pigments pigment pastes are perfect for epoxy tables, decorative designs, jewelry, and artistic castings.
4.2 How to Dose Pigment Pastes Correctly?
✔ Shake well before use – pigments may settle at the bottom of the container
✔ Add after mixing resin and hardener (A+B components)
✔ Recommended dosage: 0.5 – 5% by weight depending on the desired saturation
📌 Tip: Experiment by combining metallic pigments with pigment pastes to create unique deep color effects.
5️⃣ Alcohol Inks: Stunning Color Transitions and Abstract Patterns
5.1 How Do Alcohol Inks Work?
Alcohol inks are concentrated, alcohol-soluble dyes that create:
✔ Soft color transitions and marble-like effects
✔ Eye-catching abstract patterns on resin surfaces
✔ A “water ripple” or geode effect
5.2 How to Apply Alcohol Inks?
✔ Drop the ink directly onto the resin surface
✔ Use a heat gun or brush to spread the ink for artistic effects
✔ Combine multiple colors for dramatic contrasts
💡 Tip: Alcohol inks are not suitable for full resin coloring, but they are excellent for decorative effects.
Summary: How to Properly Pigment Epoxy Resin?
🔹 Choose the right type of pigment – solutions for transparent effects, pastes for opaque colors, metallic pigments for a luxurious look, alcohol inks for special effects
🔹 Follow the recommended dosage – start with a small amount and gradually add more
🔹 Mix thoroughly – prevent pigment settling and ensure even color distribution
🔹 Use high-quality pigments compatible with epoxy
Removing the Mold and Milling the Epoxy Resin Table: How to Achieve a Perfect Surface?
1️⃣ When and How to Remove the Epoxy Table from the Mold?
How Long Should Epoxy Cure Before Removing from the Mold?
To safely remove an epoxy table from the mold, it is essential to allow the resin to cure completely. The curing time depends on the thickness of the casting, the epoxy system used, and the surrounding temperature.
🔹 Minimum curing time before removal: 5–7 days
🔹 Recommended curing time for milling and sanding: 10–14 days
💡 Tip: If you remove the epoxy resin too soon, it may still be flexible, leading to deformation or surface damage.
How to Properly Remove an Epoxy Table from the Mold?
When removing an epoxy casting, it is important to proceed carefully to avoid damaging the mold or the table itself.
✔ Use a plastic spatula or wooden wedges to gently separate the casting from the mold
✔ Avoid sharp metal tools, which could damage the edges of the table
✔ If the mold is stuck, gently heat it with a heat gun to release the epoxy more easily
✔ Using a polypropylene mold or separation tape will make removing the epoxy table much easier
💡 Tip: If you use polypropylene separation tape, press it firmly onto the mold before pouring epoxy to prevent resin from seeping underneath the edges.
2️⃣ Milling the Epoxy Table: How to Achieve a Smooth and Even Surface?
After removing the table from the mold, the surface is often slightly uneven due to the natural shrinkage of the epoxy resin during curing. Milling helps level transitions between wood and epoxy, ensuring a perfectly flat table surface.
When is Milling Necessary?
✅ To level the surface after pouring – some areas may be uneven
✅ To remove excess resin – especially around edges or at the wood-epoxy transitions
✅ To prepare for final sanding and polishing
💡 Tip: If the epoxy resin was properly mixed and poured, surface irregularities will be minimal. However, milling is recommended for achieving maximum flatness.
How to Properly Mill an Epoxy Table?
There are several methods for milling an epoxy table, depending on the available tools:
- Hand milling with a router:Affordable, suitable for DIYers
- Requires precision and a sturdy guide frame
- CNC milling:High precision, ideal for professional production
- Higher initial cost
- Surface planer or wide belt sander:Quickly levels large surfaces
- Requires access to workshop machines
Step-by-Step Guide to Milling an Epoxy Table at Home
✔ Use a hand router with a parallel guide frame to ensure uniform milling across the entire table
✔ Secure the table firmly to a work surface to prevent movement during milling
✔ Use a wide router bit (30–50 mm) for more efficient surface processing
✔ Mill gradually in thin layers, avoiding removing too much material at once
✔ Ensure smooth movement of the router to prevent grooves and uneven spots
💡 Tip: Before milling, mark the highest point of the table to control the depth of material removal.
3️⃣ What to Do After Milling?
After successful milling, the table surface is leveled, but additional finishing steps are required to make it perfectly smooth and ready for final treatments.
How to Finish the Surface After Milling?
🔹 Sanding for a smooth finish – use progressively finer sandpaper: P80 → P120 → P240 → P400
🔹 Final polishing – for a mirror-like gloss, use special polishing pastes for epoxy
🔹 Applying a protective layer – consider oil, wax, or clear coat to enhance the colors and textures of the materials
💡 Tip: If you want to preserve the natural look of the epoxy table, use a clear protective lacquer, which highlights the colors and textures of the wood while providing long-term durability.
Summary: How to Properly Remove and Process an Epoxy Table?
✅ Mold removal: Wait at least 5–7 days, ideally 10–14 days, before removing the epoxy from the mold
✅ Use plastic or wooden tools to prevent damage to the edges of the table
✅ Milling should be done using a hand router, CNC machine, or a surface planer
✅ Gradually remove material to avoid grooves and cracks
✅ After milling, sand and polish the surface for a perfectly smooth finish
Repairing the Epoxy Tabletop After Milling – How to Achieve a Perfect Surface?
After milling an epoxy table, small defects may appear that need to be repaired before final sanding and polishing. Air bubbles, wood cracks, or uneven epoxy areas can affect both the appearance and functionality of the tabletop. Therefore, it is essential to choose the right repair method and suitable products to ensure long-term durability and an aesthetic finish.
1️⃣ Common Defects After Milling an Epoxy Table
When working on an epoxy table, various imperfections may appear that require fixing.
✅ Air bubbles in epoxy – small bubbles that become visible after milling
✅ Small cracks and fractures in the wood – natural defects that need to be filled
✅ Minor surface scratches and damage – caused by milling or handling the tabletop
💡 Tip: Make repairs immediately after milling to ensure a perfectly smooth surface before final sanding.
2️⃣ How to Fix Epoxy Resin Defects?
If small bubbles or uneven areas in epoxy appear after milling, their repair is relatively simple.
Recommended Products for Epoxy Defect Repair:
🔹 LuminaCast 1 Fast Set Primer – A fast-setting epoxy resin for minor repairs and wood sealing. Due to its low viscosity, it penetrates deep into the material and effectively seals the surface. Workability: 60-120 minutes, after which you can proceed with further processing. More about the product here
🔹 STARBOND 5-Minute Epoxy Kit – A very fast, UV-resistant epoxy resin ideal for repairing small defects in both epoxy and wood. Cures in just 5 minutes, allowing for extremely quick work. More about the product here
Steps for Fixing Epoxy Defects:
🔹 Widen the openings before filling – if the bubbles are too small, gently enlarge them with a round chisel so the epoxy can properly penetrate
🔹 Use fast-setting epoxy resin – for minor repairs, we recommend fast epoxy resin, which ensures quick filling and curing
🔹 Tint the repair epoxy – to maintain the natural look of the table, you can pigment the epoxy to match the surrounding material
🔹 Pour and check – after curing, inspect the surface and lightly sand it if necessary
💡 Tip: For a perfectly uniform surface, use LuminaCast 1 Fast Set Primer, which not only repairs defects but also seals wood pores and prepares the surface for the final epoxy layer.
3️⃣ Repairing Wood Defects in the Tabletop Using STARBOND Instant Adhesives
Wood is a natural material and may contain knots, cracks, or small voids that need to be repaired before final finishing. In such cases, STARBOND instant adhesives are the ideal solution, allowing quick and efficient repairswithout long curing times.
Advantages of STARBOND Instant Adhesives for Wood Repair:
✔ Instant curing – hardens in seconds when combined with an accelerator
✔ Versatile application – perfect for bonding, repairs, and filling cracks
✔ Strong bond strength – resistant to water, humidity, and mechanical stress
✔ Available in various viscosities and colors
STARBOND Adhesive Viscosities:
🔹 Thin (Thin CA) – low viscosity, suitable for repairing fine cracks and filling small gaps
🔹 Medium (Medium CA) – universal viscosity, ideal for standard crack repairs and bonding wooden parts
🔹 Thick (Thick CA) – high viscosity, perfect for deeper cracks and creating durable fillings
STARBOND Adhesive Color Variants:
🎨 Clear – standard transparent adhesive suitable for most repairs
🎨 Black (Black CA) – ideal for repairing dark woods and visible gap fillings
🎨 Brown (Brown CA) – a natural shade that blends seamlessly with wooden surfaces
🎨 White (White CA) – suitable for light-colored wood and surface repairs
💡 Tip: For instant curing, use STARBOND Accelerator, which reduces curing time to just a few seconds.
Summary: How to Repair an Epoxy Table After Milling?
✅ Identify defects – air bubbles, wood cracks, or uneven surfaces
✅ Use the right repair material – LuminaCast 1 Fast Set Primer, STARBOND 5-Minute Epoxy Kit, or STARBOND instant adhesives
✅ Allow the repaired surface to cure and then lightly sand it
🔹 Want to achieve a flawless epoxy table? Use LuminaCast 1 Fast Set Primer for repairs and wood sealing, STARBOND 5-Minute Epoxy Kit for ultra-fast epoxy repairs, or STARBOND instant adhesives for wood repair and fine details.
Sanding an Epoxy Table: How to Achieve a Perfectly Smooth Surface?
Sanding epoxy resin is a crucial step to achieving a smooth, glossy, and professional finish. The right technique and choice of abrasives significantly impact the final surface quality and long-term durability. This comprehensive guide to sanding epoxy resin tables will help you understand how to sand an epoxy table step by step and which products to use for the best results.
1️⃣ How to Properly Sand an Epoxy Table?
Sanding epoxy resin consists of several stages – from rough surface leveling to fine polishing that ensures a flawless shine. Each step is essential for achieving an optimal finish.
What Affects the Choice of Abrasives?
✔ Type of Finish – Do you want a matte, satin, or glossy surface?
✔ Table Material – A combination of wood and epoxy requires a different approach than a fully epoxy table.
✔ Protective Coating Used – If you plan to apply oil or wax, sanding wood to a lower grit is essential for proper absorption.
💡 Tip: When sanding epoxy resin, it is essential to follow gradual grit steps and not skip grits to avoid leaving visible marks.
2️⃣ Choosing the Right Tools and Abrasives for an Epoxy Table
🔹 Best Sander for Epoxy Resin – An orbital sander with a random orbital motion allows smooth and even sanding.
🔹 Professional Abrasives – KOVAX Japanese sanding discs for maximum efficiency and dust removal.
🔹 Proper Interface Pads – Using a micro hook & loop pad ensures smoother transitions between grit levels.
📌 Recommended Sanding Systems:
✅ KOVAX Tri-Pro or Super Assilex (for coarse sanding 80–400)
✅ KOVAX Super Assilex (for fine sanding 600–1500)
✅ KOVAX Buflex Dry (for finishing sanding 2000–3000)
💡 Tip: KOVAX abrasives are anti-static, reduce clogging, and leave minimal sanding marks.
3️⃣ Step-by-Step Guide to Sanding Epoxy Resin
3.1 Coarse Sanding (80–400) – Removing Irregularities and Leveling the Surface
✔ Use KOVAX TRI-PRO sanding discs with 8 or 15 holes and grits K80–K400
✔ Start with coarse grit (K80) and gradually move to finer (K400)
✔ Check each step thoroughly to ensure there are no deep scratches
✔ Do not skip grit levels, as this may result in visible sanding marks
💡 Tip: Use an orbital sander with a firm interface pad to apply even pressure across the entire surface.
3.2 Fine Sanding (600–1500) – Preparing for Final Polishing
✔ Use KOVAX Super Assilex abrasives in grits K600, K800, K1200, and K1500
✔ Fine sanding smooths the epoxy surface and prepares it for polishing
✔ Always remove dust before switching to a higher grit to avoid scratches
💡 Tip: If applying oil or wax, sand wood only up to K320 to allow proper absorption.
3.3 Final Sanding & Polishing (2000–3000) – Achieving a Mirror-Like Finish
✔ Use KOVAX Buflex Dry in grits K2000, K2500, and K3000
✔ Fine sanding eliminates the last micro-scratches and prepares the surface for polishing
✔ After completing this step, the epoxy surface will be nearly transparent
💡 Tip: For ultimate surface clarity, polish the epoxy resin with a specialized polishing compound.
4️⃣ Polishing the Epoxy Table – How to Achieve a Mirror-Like Shine?
After thorough sanding, the final step is polishing the epoxy resin. This enhances the gloss and highlights the depth and details of the surface.
📌 Recommended Polishing System:
✅ FINIXA Polishing Compound – A specially formulated polish for epoxy resin
✅ Polishing Pads – Use an orange pad for perfect buffing
✅ Rotary Polisher – Maximum speed of 300 RPM to prevent overheating
💡 Tip: Once polished, your table will have a flawless mirror-like reflection, accentuating the beauty of the wood and epoxy.
Summary: How to Properly Sand and Polish an Epoxy Table?
✅ Start with coarse sanding (K80–K400) – Removing surface irregularities
✅ Fine sanding (K600–K1500) – Smoothing the surface before polishing
✅ Final sanding (K2000–K3000) – Achieving ultimate smoothness and gloss
✅ Polishing with FINIXA compound – For a stunning mirror-like finish
🔹 Want to achieve a perfect epoxy table? Use an orbital sander, KOVAX abrasives, and professional polishing compounds for the best possible results.
Protecting Your Epoxy Resin Tabletop: How to Ensure Long-Lasting Durability and Resistance?
Epoxy resin tabletops are a luxurious and durable interior feature, but they require proper surface treatment and protection to maintain their flawless appearance for years. There are several protection methods, each with its own advantages depending on how the table will be used.
🔹 Which protection method should you choose?
✔ Oiling – natural look, ideal for food contact
✔ Ceramic coating – an additional protective layer compatible with oil, wax, and lacquer
✔ Lacquering – universal protection with matte or glossy finishes
1️⃣ Protective Oils for Wood and Epoxy Resin
If you’re looking for natural protection that also enhances the wood grain, oiling is the perfect solution.
💡 When to choose oiling?
✔ If you want a natural wood appearance
✔ If the table will come into contact with food (e.g., serving boards)
✔ If you prefer a matte to satin finish
📌 Recommended Product: Rubio Monocoat Oil Plus 2C
✅ Certified for food contact
✅ Single-layer system – no need for multiple coats
✅ High resistance to water and stains
How to properly apply Rubio Monocoat on an epoxy table?
🔹 1. Thoroughly sand and clean the surface
🔹 2. Mix the oil with the accelerator at a 3:1 ratio
🔹 3. Apply the oil with a cloth, sponge, or pad
🔹 4. Wipe off excess oil after 10–15 minutes
🔹 5. Let the surface cure for 24–36 hours
💡 Tip: Regularly refresh the protection with Rubio Monocoat Refresh.
2️⃣ Ceramic Coating: An Additional Protective Layer for Maximum Durability
🔹 Can be applied not only on epoxy but also over oiled, waxed, and lacquered surfaces
🔹 Creates an ultra-hydrophobic layer and protects against scratches
🔹 Extends the lifespan of the surface by several years
💡 Why choose ceramic protection?
✔ Scratch and UV resistance – keeps the surface looking new longer
✔ Increased resistance to chemicals and stains
✔ Compatible with all surface finishes – epoxy, wood, oil, lacquer, and wax
📌 Recommended Product: Ice Epoxy Graph Ice 9H+
✅ 9H+ hardness – extreme resistance to mechanical damage
✅ Protects epoxy, wood, and lacquered surfaces
✅ Long-lasting protection – up to 3 years
How to properly apply ceramic protection?
🔹 1. Clean and dry the surface
🔹 2. Apply the ceramic coating with a sponge
🔹 3. Wait 2 minutes, then gently buff with a microfiber cloth
🔹 4. For maximum hardness, cure with infrared light (80°C for 30 minutes)
🔹 5. Full ceramic curing takes 72 hours
💡 Tip: If you already have the surface treated with oil, wax, or lacquer, the ceramic coating will provide extra protection and extend its durability.
3️⃣ Lacquering the Epoxy Table
Lacquering provides traditional and universal protection, allowing for various levels of gloss.
💡 Why choose lacquering?
✔ Suitable for both indoor and outdoor use
✔ Choice of matte, satin, or glossy finishes
✔ Long-term protection against moisture and mechanical damage
📌 Recommended Products:
✅ Polyurethane Lacquers – moisture-resistant and durable
✅ Acrylic Lacquers – quick-drying, ideal for interiors
✅ UV-Stable Lacquers – prevent epoxy resin from yellowing
How to properly lacquer an epoxy table?
🔹 1. Sand the surface with P400–P600 grit
🔹 2. Apply the first thin coat of lacquer and let it dry
🔹 3. After 24 hours, lightly sand and apply a second coat
🔹 4. Allow the lacquer to cure for at least 48 hours before use
💡 Tip: For maximum protection, combine wood oiling with epoxy lacquering.
Conclusion: How to Best Protect Your Epoxy Table?
✅ Oiling – natural look, certified for food contact
✅ Ceramic coating – an extra layer of protection, compatible with oil, lacquer, and wax
✅ Lacquering – universal protection with different gloss levels