Den Braven EPOXIN F1000 DRY 4,4 Kg
Code: 7802/004400Related products

Universal cleaning spray with 99.9% isopropyl alcohol for perfect degreasing and removal of dirt from electronics, glass, metal, plastic, and tools. Fast-drying, residue-free,...

Construction polypropylene tape for the production of epoxy molds. Length 55m, width 60mm

High quality polypropylene tape for excellent separation of casting from mold, 48 mm x 66 m

Single-component solution designed for effective and quick removal and cleaning of surfaces from grease, oil, wax, dust, and similar contaminant.
Product detailed description
EPOXIN F1000 DRY - 2K epoxy penetrating coating for dry substrates
EPOXIN F1000 DRY is a two-component epoxy primer designed for dry substrates with a maximum moisture content of up to 4%. This low-viscosity material without solvents and nonylphenol ensures excellent adhesion and mechanical resistance of the substrate. It is ideal for surface preparation before applying epoxy flooring systems, where it unifies the absorbency of the substrate and fills pores and capillaries.
Technical specifications
- Base: Epoxy resin
- Consistency: Low-viscosity liquid
- Color: Transparent
- Density: 1.1 kg/l (at 20 °C)
- Application temperature: +10 °C to +30 °C
- Curing time: 24 hours (at 20 °C)
- Consumption: 0.4 kg/m²
- Packaging: 4.4 kg (A + B) (A = 3.0 kg; B = 1.4 kg)
Key properties
- High adhesion: Ensures a strong bond with the substrate.
- Mechanical resistance: Enhances the substrate’s resistance to mechanical stress.
- Low VOC emissions: Environmentally friendly.
- Solvent and nonylphenol-free: Safe for users.
- Fills pores and capillaries: Prepares the surface for subsequent layers.
- Quick curing: Enables fast work progression.
EPOXIN F1000 DRY is suitable for application on cement-based substrates, serving as a capillary seal to create an impermeable and reinforced layer. It is ideal for substrate preparation before applying EPOXIN flooring systems and can form a scratch coat and leveling layer when combined with quartz sand.
- Penetration of cement substrates with capillary sealing of the base
- Penetration of cement substrates to create an impermeable and reinforced layer
- Preparation of the substrate for EPOXIN flooring systems
- Forms a scratch coat and leveling layer when combined with quartz sand
Application Information
Application Conditions
EPOXIN F1000 DRY must not be applied at ambient and substrate temperatures below +10 °C or above +30 °C. At temperatures below +10 °C, viscosity increases. The recommended application temperature is +20 °C with an optimal air humidity of 65%. During application and curing, EPOXIN F1000 DRY must not come into contact with water or other chemical loads – the substrate temperature must be at least +3 °C above the dew point. These conditions should be maintained throughout the application and curing process.
Substrate Preparation
The substrate must be cleaned, free of all non-cohesive parts, and roughened, e.g., by shot blasting, grinding, milling, etc., with thorough vacuuming of all loose particles. The substrate must be free of dust, grease, and other contaminants that could act as separators. The surface must not have rising moisture to prevent blistering or pores. Any unevenness, cracks, and other defects must be repaired. The residual moisture content of the substrate must not exceed 4%. The pull-off strength of the substrate surface layer must be greater than 1.5 N/mm². The minimum compressive strength of the concrete substrate must be 25 N/mm².
Application Procedure
EPOXIN F1000 DRY is supplied in the correct mixing ratio. It is essential to thoroughly mix component A with component B by pouring component B into component A (for the colored version, component A should be mixed first before adding component B). Use a clean, slow-speed mixer (300–400 rpm) for thorough mixing. The mixture should then be transferred to a clean container and mixed again for 2–3 minutes to achieve a uniform appearance. Care must be taken to avoid air entrapment during mixing (do not store the mixed material in large amounts or re-mix after 5–10 minutes, as this may lead to a rapid exothermic reaction). The prepared material must be applied during its pot life using suitable technology, such as brush, roller, rubber squeegee, notched trowel, airless spraying, etc. (the appropriate application method should be tested before starting). If the substrate is not completely sealed with the primer, defects in subsequent layers may occur, requiring multiple primer coats for complete sealing.
Up to 50% by weight of clean, dry silica sand with a grain size of 0.1–0.3 mm can be added to EPOXIN F1000 DRY for scratch coats (fine leveling mortar for surface irregularities < 1 mm). Up to 100% by weight of clean, dry silica sand with a grain size of 0.1–0.3 mm can be added to create a scratch coat (leveling mortar for surface irregularities < 2 mm). EPOXIN F1000 DRY can also be used as a leveling screed (1 part by weight of EPOXIN F1000 DRY + 10 parts by weight of silica sand) with a suitable combination of clean, dry silica sands (repair screed for surface irregularities of 15–20 mm). For leveling screeds, we recommend using the following sand mixture: 25% particle size 0.1–0.5 mm; 25% particle size 0.3–0.8 mm; 25% particle size 0.8–1.2 mm; 25% particle size 2.0–4.0 mm (suitable for layer thicknesses of 15–20 mm, with the largest particle size not exceeding 1/3 of the total layer thickness). Silica sands and other fillers should be added to the mixed binder while stirring continuously. The mixture must be well mixed to avoid lumps and filler clumps. Application of screeds and scratch coats should be done using a trowel, rubber squeegee, or notched trowel, with the size of the notches chosen based on the required layer thickness.
After application, the surface must be protected from direct contact with water for at least 24 hours. During this time, the air temperature must be 3 °C above the dew point. Contact with water during this period may cause white spots and a sticky surface.
Warning
This product is intended for professional use only. The material should be used in a single operation. At high ambient temperatures or underfloor heating and high continuous loads, visible impressions on the floor (shelves, furniture, etc.) may occur. It is recommended to apply the primer during a temperature decrease to avoid open pores caused by rising air in the substrate. These potential open pores should be treated with a scratch coat of EPOXIN F1000 DRY and approximately 3% THIXOP. For heated spaces, do not use fuel, gas, or wood heaters during application as CO2 and water vapor can adversely affect the surface quality. Electric heaters are recommended for heating.
All data in this technical sheet are non-binding but have been prepared according to the best knowledge and practical experience and are based on the latest technical findings. The product must not be modified or used contrary to this technical sheet.
Additional parameters
Category: | Epoxy Resins |
---|---|
Weight: | 5 kg |
EAN: | 8595100143976 |
Color: | Transparent |
Type of use: | Penetrates, Undercoat, Floors, Sealing of Floors |

Clear casting epoxy resin with maximum UV protection, casting thickness 1 - 20 mm, workability approx. 45 min, highly viscous - thick, safe for contact with food, mixing ratio...
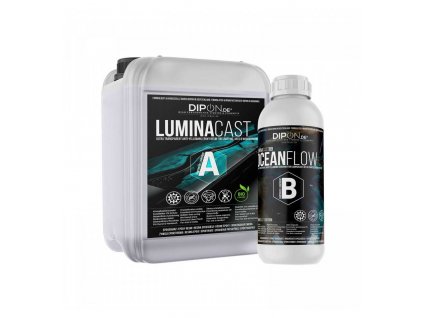
Clear casting epoxy resin with food contact certification with maximum UV protection, casting thickness up to 10 cm, workability up to 240 min, low-viscosity (liquid),...
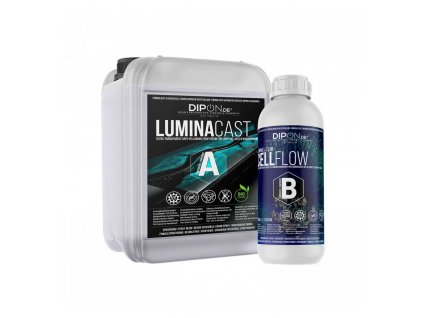
Clear casting epoxy resin with maximum UV protection, casting thickness 1 - 20 mm, workability about 50 min, medium viscosity, mixing ratio 2:1 by weight.

Clear casting epoxy resin for small castings, casting thickness 0.1 - 2 cm (at max 22 °C), cures from 15 °C, hardness 83 SHORE D, VOC 0 g/L, mixing ratio by weight 2:1, can be...

Clear casting epoxy resin for small castings, casting thickness 0.1 - 2 cm (at max 22 °C), cures from 15 °C, hardness 83 SHORE D, VOC 0 g/L, mixing ratio by weight 2:1, can be...

Clear casting epoxy resin for large castings, casting thickness up to 10 cm (at max 20 °C), cures from 10 °C, hardness 77 SHORE D, VOC 0 g/L, mixing ratio by weight 2:1, full...

Clear casting epoxy resin with maximum UV protection, casting thickness 1 - 10 mm, workability approx. 35 min, particularly low viscosity (very liquid), safe for contact with...

Clear casting epoxy resin with maximum UV protection, casting thickness 1 - 10 mm, workability approx. 35 min, particularly low viscosity (very liquid), safe for contact with...

Crystal clear casting epoxy resin with maximum UV protection, casting thickness 1 - 20 mm, workability approx. 50 min, almost medium viscosity (liquid - medium liquid), safe for...

Clear casting epoxy resin with maximum UV protection, casting thickness 1 - 20 mm, one and a half times higher viscosity than LuminaCast 4 Gem Flow, workability approx. 60 min,...
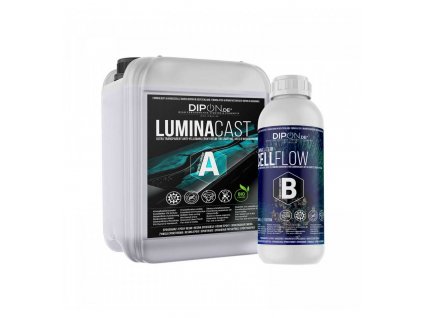
Clear casting epoxy resin with maximum UV protection, casting thickness 1 - 20 mm, workability about 50 min, medium viscosity, mixing ratio 2:1 by weight.
Be the first who will post an article to this item!
Be the first who will post an article to this item!