DIPON Epoxyplast 3D B100 ULTRAPOUR - Part B hardener
Code: 6427/000250 6427/000500 6427/001000 6427/002500 6427/005000 Choose variantRelated products

Epoxy resin (component A) for EPOXYPLAST B20 Jewel Cast, EPOXYPLAST B50 Deep Pour, EPOXYPLAST B100 Ultra Pour
Product detailed description
!!! Only Epoxyplast 3D B50 hardener (does not contain epoxy resin - Component A) !!!
Note that this is a single component epoxy resin without a hardener. It is necessary to purchase Epoxyplast 3D - Component A separately or to purchase epoxy resin with hardener directlyDIPON EpoxyPlast 3D B100 Ultra Pour
EpoxyPlast 3D B100 Ultra Pour is a premium epoxy resin designed for applications requiring a maximum casting depth of up to 10 cm. Thanks to its low viscosity, it ensures excellent flow and the ability to reach even the smallest details. Ideal for furniture production, table casting, lamp design, and large-scale artistic projects.
This resin boasts a crystal-clear appearance, high gloss, and resistance to yellowing due to advanced UV protection technology with UV absorbers and HALS additives. Its eco-friendly formulation contains over 70% biodegradable components, contributing to sustainable creation. EpoxyPlast 3D B100 Ultra Pour is the key to perfect results in deep casting projects requiring precision, durability, and aesthetic excellence.
With a long working time of approximately 240 minutes at 23 °C, this resin is suitable for demanding projects requiring slow curing. This feature prevents overheating and allows the creation of smooth, bubble-free surfaces. The mixing ratio 2:1 by weight and the recommended layer thickness 3–10 cm make this resin an ideal material for professionals and creative makers.

Key Features
- Pouring depth up to 10 cm in one step (at 20 °C).
- Crystal clarity for artistic and decorative projects.
- Advanced UV additives protect against yellowing and UV damage.
- Low viscosity ensures excellent flow and smooth, bubble-free surfaces.
- Long working time of approximately 240 minutes for large projects.
- Environmentally friendly formulation contains more than 70% biodegradable components.
- Mechanical strength of 81 Shore D and heat resistance up to 63 °C.
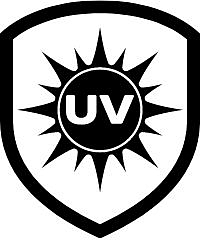
UV resistant
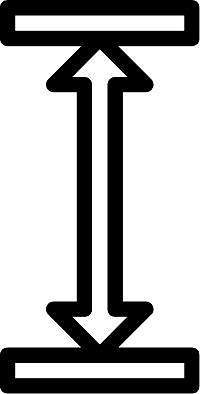
Solid castings up to 10 cm
It enables casting of massive castings up to 10 cm thick (at 20°C).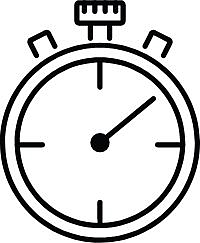
Processing time up to 3 hours
The long processing time of up to 3 hours provides sufficient time for mixing, pigmentation and de-bubbling of the mixture.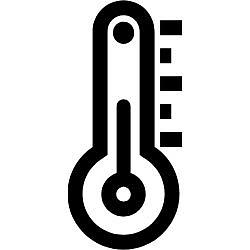
Cures at temperatures from 10 °C
It cures at low temperatures as low as 10 °C, which is appreciated by everyone, especially in the winter months, when heating production areas is costly.High-quality epoxy resin for River Tables
EpoxyPlast 3D B100 Ultra Pour is specially designed for crafting impressive River Tables and for use in large silicone molds. It allows for a pouring height of up to an impressive 100 mm at 20°C. Remember, higher casting heights are possible depending on the room temperature and the amount of material, provided it's lower than 20°C.General Characteristics
- Stable formulation against crystallization
- Very slow heat development during curing
- Very long processing and curing time
- Low viscosity for optimal flow
- Contains UV absorbers and n-HALS light stabilizers
- Ideal for large-volume casting, such as River Tables
- High resistance to carbamates
- Highly transparent glass-like hardness after curing
- Excellent self-deaerating properties
- Bio-based components in epoxy resin
- Free from hazardous substances listed in CoRAP and sVHC
- Latest base amines and additives with minimal yellowing
- 0 % VOC (EU values)
- Exceptional wetting properties for various surfaces
- Very low shrinkage (<0.1 %)
- Compatible with wood, concrete, glass, metal, glass and carbon fibers, natural stone, quartz sand, marble, and granite
Key Application Data
- Mixing ratio: 2:1 (A+B) by weight
- Dynamic viscosity at 23 °C:
- Component A: 580 ± 50 mPa·s
- Component B: 55 ± 25 mPa·s
- Layer thickness (20 °C): 30 - 100 mm
- Processing time (23 °C, 500 grams, 90 mm): approx. 240 minutes
- Maximum exothermic reaction (tTmax, 23 °C, 500 grams, 90 mm): approx. 480 minutes
- Recommended material temperature A+B: min. 20 °C, recommended 23 °C
- Recommended ambient temperature: min. 10 °C, recommended 12 °C - 19 °C
- Recommended casting height (20 °C): 3 cm - 10 cm (30 - 100 mm)
- Demoldable after (23 °C): approx. 96 hours (50 mm)
- Next layer applicable after (20 °C): approx. 36 hours (50 mm)
- Sandable after: approx. 10 days (80 mm, 20 °C)
- Minimum mixing quantity (A+B): 120 grams
- Minimum casting height: 3 cm (30 mm)
- Hardness after 7 days (23 °C):Shore D81
- Heat resistance: approx. 63 °C
Areas of Application
- Ideal for large-scale projects: EpoxyPlast 3D B100 Ultra Pour is specifically designed for the creation of impressive River Tables and use in large silicone molds.
- Excellent for furniture making: Allows casting heights from a minimum of 30 mm up to 100 mm at 20 °C.
- Safe for food contact: The formulation is free from substances listed in sVHC or CoRAP. After complete curing, the product is suitable for contact with food.
- Higher casting heights above 100 mm: Higher casting volumes are possible depending on the material quantity and ambient temperature, provided it is significantly below 20 °C.
Recommended minimum mixed amount 90 grams
*If the amount of mixture falls below the minimum of 90 grams, the curing time may be extended. It is also possible to create a mass that is not completely homogeneous and the exothermic reaction is too low to completely harden the workpiece. The recommended minimum amount of mixture is 90 grams (A 60 grams + B 30 grams), the recommended amount is 120 grams (80 grams A + 40 grams B).What is EpoxyPlast 3D?
- EpoxyPlast 3D was developed in 2019 as a self-venting system that is easy to use and covers a wide range of applications, especially in the artistic field.
- Since its launch, it has become a popular choice among users, particularly EpoxyPlast 3D B20 Jewel Cast, which has been used by more than 100,000 users since 2019. Additionally, the well-known thick-film systems, such as EpoxyPlast 3D B50 Deep Pour and EpoxyPlast 3D B100 Ultra Pour – the first systems in Germany capable of casting up to 10 cm in depth – have also proven highly effective.
- These epoxy systems have been applied hundreds of thousands of times with outstanding results, demonstrating their reliability and ability to create perfect surfaces for demanding projects.
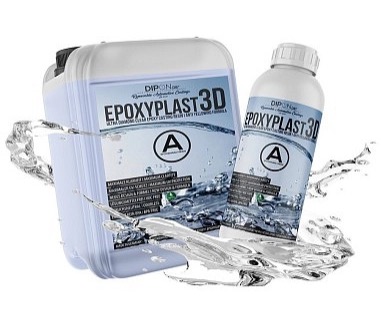
EpoxyPlast 3D (component A: 580 ± 50 mPa*s, 23 °C) consists of one resin and three hardeners.
Typ | *Dyn. viskozita 23 °C (mPa*s) | **Zpracovatelnost: 200g, 23 °C - 40 °C | Max. síla odlitku | Použití | UV odolnost |
---|---|---|---|---|---|
EpoxyPlast 3D B20 Jewel Cast | 800 ± 50 | cca 55 min | 0,1 mm - 20 mm | Art & Vložení | Excelentní |
EpoxyPlast 3D B50 Deep Pour | 75 ± 25 | cca 180 min **500 gramů, 5cm | 20 mm - 50 mm | Zalévání silných odlitků | Excelentní |
EpoxyPlast 3D B100 Ultra Pour | 50 ± 25 | cca 240 min **500 gramů, 9cm | 30 mm - 100 mm | Zalévání silných odlitků | Excelentní |
*Dynamická viskozita se měří při 23°C. Snížení teploty materiálu je doprovázeno neúměrným zvýšením dyn. viskozity. To je eminentně důležité, zejména pokud jde o samoodvzdušňování.
**Doba zpracování je uvedena pro směs 200 gramů v mixovací nádobě (průměr 5 cm). Doba zpracování = teplota materiálu 23°C -> 40°C = zdvojnásobení počáteční viskozity. Čas na maximální exotermickou teplotu (tTmax) je obvykle dvojnásobkem doby zpracování.
- EpoxyPlast 3D Složka A - epoxidová pryskyřice pro všechna tvrdila EpoxyPlast 3D - (580 mPa*s ± 50, 23°C)
- EpoxyPlast 3D B20 Jewel Cast - Nízká viskozita, zpracovatelnost cca 55 min, pro drobné odlitky.
- EpoxyPlast 3D B50 Deep Pour- Nízká viskozita, pro velké tlustovrstvé odlitky, např. pro říční stoly, výrobu lamp, větší odlitky v jednom lití.
- EpoxyPlast 3D B100 Ultra Pour - Nízká viskozita, pro velmi velké tlustovrstvé odlitky, např. pro říční stoly, výrobu lamp.
How to use
Application and Usage
- Check the ambient temperature, as it's the most critical parameter alongside the casting volume. Successful application depends on room temperature and the amount/volume of the resin and hardener mix used. An excessively high room temperature can lead to a very strong exothermic reaction, resulting in yellowing, cracking, and vapor formation in the mixture.
- Before use, perform a preliminary test for material compatibility to be painted/poured.
- The recommended procedure for the most accurate measurement of all components is by weight, precisely weighing in a 100:50 or 2:1 weight parts ratio based on component (A). Even a slight deviation results in extended or non-occurring hardening. Adding too much hardener increases the material's elasticity and decreases its SHORE D hardness. Excess of component A results in a permanently sticky film, non-reversible due to polyaddition. The maximum deviation in the tolerance range is 0.1%.
- Adhere to the recommended mixing time of three to four minutes, then pour into a clean container and mix again for three to four minutes to achieve a maximally homogeneous mixture.
- Use the mixing container only once. Follow the recommended maximum mixing speed for both components, which is 300 rpm, preventing or minimizing the formation of air pockets during mixing. Manual mixing is recommended for smaller quantities up to approx. 1 kg. Due to its extended work time, it degasses excellently. We recommend using Allway Tools Helix for mixing.
- To prevent resin seepage due to the prolonged curing time, ensure complete sealing of the mold. Suitable for this is the DIPON polypropylene tape, which can be easily separated from the mold after hardening. Optionally, a release wax can be used.
Cleaning
- For cleaning used applicators, use acetone or universal thinner. Once the epoxy resin hardens, it can only be removed by sanding. Cleaning immediately after use is recommended.
Important Note:
- Mixing transport containers (bottles/cans) A (resin) and B (hardener) will result in incomplete hardening and the corresponding incorrect result. Always weigh both components precisely.
- The higher the room temperature and the larger the mixed quantity, the faster the exothermic reaction.
Additional parameters
Category: | Individual Components of Epoxy Resin and Hardeners |
---|---|
EAN: | Choose variant |

Clear casting epoxy resin for large castings, casting thickness up to 10 cm (at max 20 °C), cures from 10 °C, hardness 77 SHORE D, VOC 0 g/L, mixing ratio by weight 2:1, full...

Clear casting epoxy resin for large castings, casting thickness up to 10 cm (at max 20 °C), cures from 10 °C, hardness 81 SHORE D, VOC 0 g/L, mixing ratio by weight 2:1, full...

Clear casting epoxy resin for large castings, casting thickness up to 10 cm (at max 20 °C), cures from 10 °C, hardness 81 SHORE D, VOC 0 g/L, mixing ratio by weight 2:1, full...

Clear casting epoxy resin for large castings, casting thickness up to 10 cm (at max 20 °C), cures from 10 °C, hardness 81 SHORE D, VOC 0 g/L, mixing ratio by weight 2:1, full...

Clear casting epoxy resin for large castings, casting thickness up to 10 cm (at max 20 °C), cures from 10 °C, hardness 81 SHORE D, VOC 0 g/L, mixing ratio by weight 2:1, full...
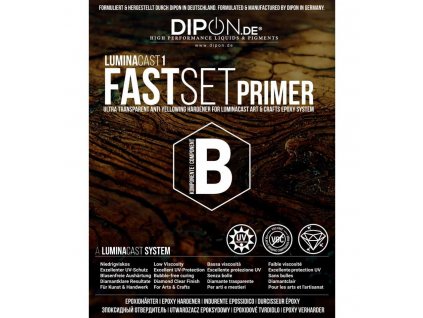
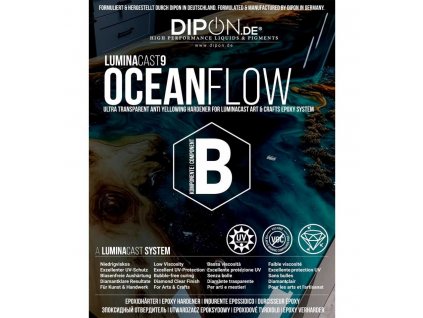
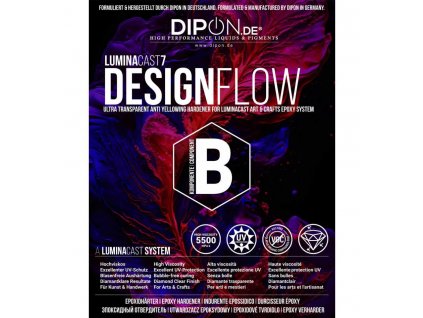

Hardener for Epoxyplast 3D resin designed for medium castings thickness 0.1 - 5 cm (at max 20 °C), cures from 15 °C, hardness 81 SHORE D, VOC 0 g/L, mixing ratio by weight 2:1,...
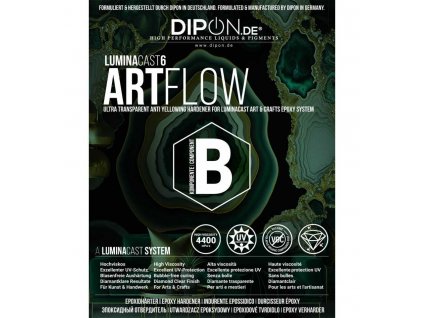
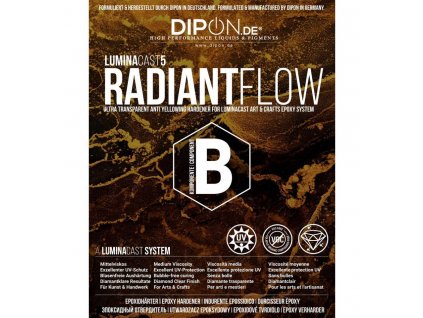
Be the first who will post an article to this item!
Be the first who will post an article to this item!
Manufacturing company : | DIPON.DE Removable Automotive Coatings GmbH & Co. |
---|---|
Address : | Ringofenstr. 39 I 44287, Dortmund, Deutschland |
E-mail : | info@dipon.de |