DIPON LuminaCast 9 Ocean Flow - Part B
Code: 7239/000250 7239/000500 7239/001000 7239/002500 7239/005000 Choose variantProduct detailed description
!!! Only LuminaCast hardener Component B (does not contain epoxy resin - Component A) !!!
Note that this is a separate claim for epoxy resin. It is necessary to purchase LuminaCast epoxy resin - Component A separately or to purchase epoxy resin with hardener directly.DIPON LuminaCast 9 Ocean Flow
LuminaCast 9 Ocean Flow is a low viscosity crystal-clear epoxy resin boasting high transparency. This casting epoxy resin has been specially developed for large casting projects, including epoxy river tables, designer furniture, lamps, and more.
Are you in search of a high-quality epoxy resin with an extended work time? LuminaCast 9 Ocean Flow offers the capability to cast up to 10 cm thick layers in a single step. With a refractive index of > 1.59, this product stands among the most transparent epoxy resins on the market.
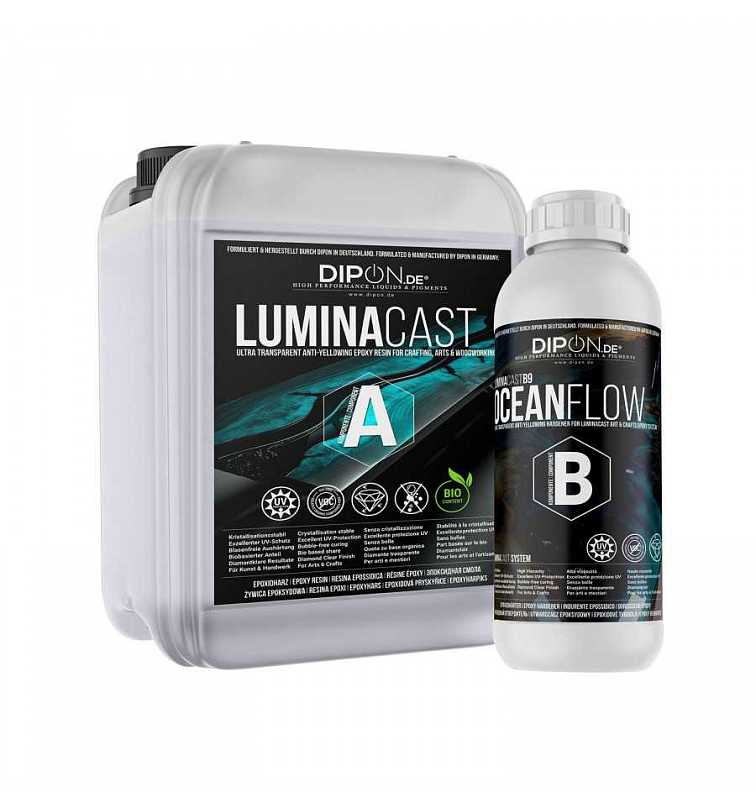
Key features of LuminaCast 9 Ocean Flow casting resin
- Mixing ratio 2:1 by weight.
- Casting height up to 10 cm and an extended work time of up to 240 minutes, depending on the quantity and ambient temperature.
- Food contact certificate 1935/2004 EC
- Optimized for furniture makers for casting tables, lamp production, or jewelry where a greater casting height is required.
- Demolding possible after 72 - 96 hours (23°C).
- Can be sanded after a minimum of 8 days (20°C).
- Creates an incomparably smooth and glossy surface.
- Advanced composition minimizes carbamate formation and ensures a flawless surface without blemishes.
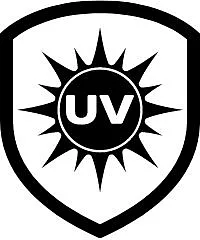
Maximum UV protection
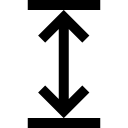
Casting height up to 10 cm
Up to 10 cm (20°C) in a single pour, depending on the amount of material and ambient temperature.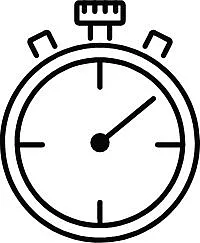
Workability up to 4 hours
Extended workability provides ample time for mixing, pigmenting, and degassing the mixture (at 23°C, 500g, 90mm).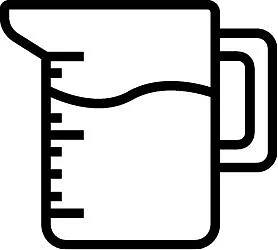
Mixing ratio 2:1 by weight
Very easy mixing and calculation of the correct amount of individual components.High-quality epoxy resin for River Tables
LuminaCast 9 Ocean Flow is specially designed for crafting impressive River Tables and for use in large silicone molds. It allows for a pouring height of up to an impressive 100 mm at 20°C. Remember, higher casting heights are possible depending on the room temperature and the amount of material, provided it's lower than 20°C.General Characteristics
- Crystallization stable
- Bio-based ingredients in the epoxy resin
- Free from CoRAP and sVHC substances
- State-of-the-art base amines and additives with particularly low yellowing tendencies
- Mixing ratio: 2:1 by weight
- Pot life (23°C), 500 grams, 9 cm: approx. 240 min. (23°C- > 40°C)
- Recommended material temperature (A+B): 20°- 24°C
- Recommended ambient temperature: 15°C - 20°C
- Dyn. Viscosity (mPa*s) 23°C: A 730 ± 50
- Dyn. Viscosity (mPa*s) 23°C: B 55 ± 25
- Diamond Clear transparency
- Layer thickness (23°C): 30 - 100 mm
- 0% VOC content
- Excellent substrate wetting capability
- Very low shrinkage (<0.1%)
- Compatible with, e.g., wood, concrete, glass, metal, glass and carbon fiber fabrics, natural stone, quartz sand, marble, granite
Key Application Data
- Pot life at 23°C (500 grams, 90 mm): approx. 240 min.
- Time to max exothermy (tTmax) (23°C, 500 grams, 90 mm): approx. 480 min.
- Mixing duration: 3-4 min. + transfer and another 3-4 min for a uniform mixture
- Mixing ratio: 2:1 by weight
- Recommended casting height (20°C): 3.0 cm - 10.0 cm (30 - 100 mm)
- Demoldable after (23°C): approx. 72 - 96 hrs.
- Next layer pourable after: approx. 28 - 36 hrs. at 20°C, 50 mm
- Minimum recommended mixing amount: 120 grams A+B
- Sandable after: min. 8 days, 100 mm, 20°C
How to use
Application and Usage
- Check the ambient temperature, as it's the most critical parameter alongside the casting volume. Successful application depends on room temperature and the amount/volume of the resin and hardener mix used. An excessively high room temperature can lead to a very strong exothermic reaction, resulting in yellowing, cracking, and vapor formation in the mixture.
- Before use, perform a preliminary test for material compatibility to be painted/poured.
- The recommended procedure for the most accurate measurement of all components is by weight, precisely weighing in a 100:50 or 2:1 weight parts ratio based on component (A). Even a slight deviation results in extended or non-occurring hardening. Adding too much hardener increases the material's elasticity and decreases its SHORE D hardness. Excess of component A results in a permanently sticky film, non-reversible due to polyaddition. The maximum deviation in the tolerance range is 0.1%.
- Adhere to the recommended mixing time of three to four minutes, then pour into a clean container and mix again for three to four minutes to achieve a maximally homogeneous mixture.
- Use the mixing container only once. Follow the recommended maximum mixing speed for both components, which is 300 rpm, preventing or minimizing the formation of air pockets during mixing. Manual mixing is recommended for smaller quantities up to approx. 1 kg. Due to its extended work time, it degasses excellently. We recommend using Allway Tools Helix for mixing.
- To prevent resin seepage due to the prolonged curing time, ensure complete sealing of the mold. Suitable for this is the DIPON polypropylene tape, which can be easily separated from the mold after hardening. Optionally, a release wax can be used.
Cleaning
- For cleaning used applicators, use acetone or universal thinner. Once the epoxy resin hardens, it can only be removed by sanding. Cleaning immediately after use is recommended.
Important Note:
- Mixing transport containers (bottles/cans) A (resin) and B (hardener) will result in incomplete hardening and the corresponding incorrect result. Always weigh both components precisely.
- The higher the room temperature and the larger the mixed quantity, the faster the exothermic reaction.
Calculation of the amount of epoxy resin
📌 Calculator for determining total resin quantity:
✅ Enter length × width × height (in cm or meters)
✅ The calculator converts volume to liters or kilograms based on resin density
📌 Calculator for calculating components A and B based on mixing ratio:
✅ Enter total weight or volume of resin
✅ The calculator determines the exact amount of components A and B
Recommended minimum mixed amount 90 grams
*If the amount of mixture falls below the minimum of 90 grams, the curing time may be extended. It is also possible to create a mass that is not completely homogeneous and the exothermic reaction is too low to completely harden the workpiece. The recommended minimum amount of mixture is 90 grams (A 60 grams + B 30 grams), the recommended amount is 120 grams (80 grams A + 40 grams B).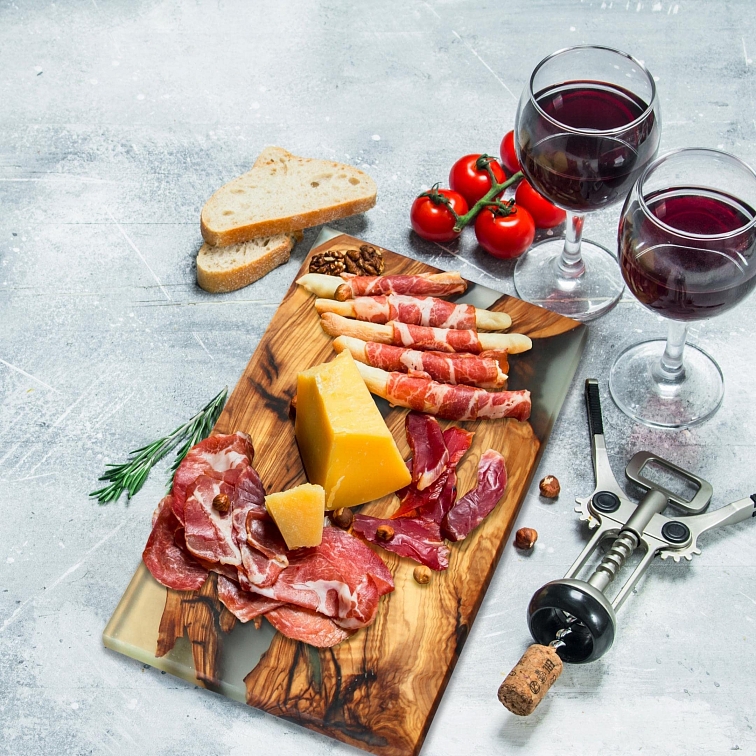
Food-safe?
The formula contains no substances of SVHC or CoRAP. After complete chemical curing, approximately 14 days at 25°C, the product is suitable for food contact.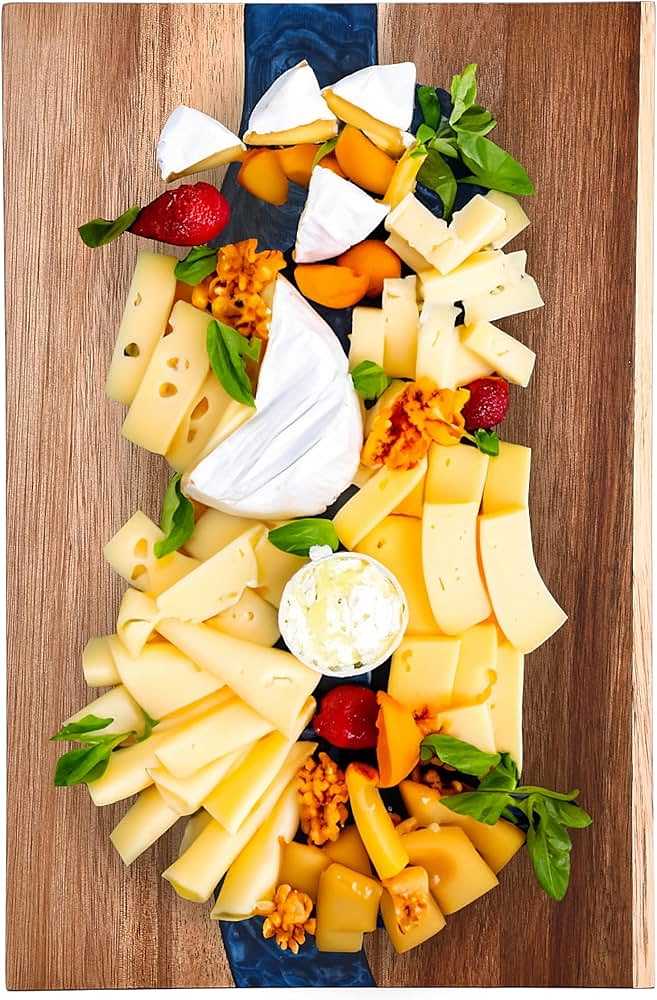
LuminaCast – Certified for Safe Food Contact According to Regulation 1935/2004 EC
The LuminaCast 9 Ocean Flow epoxy resin has received official certification for food contact in accordance with Regulation 1935/2004 EC, confirming its safety and non-toxicity when in contact with food. Thanks to this certification, all other LuminaCast epoxy resins, which share the same composition and properties, are also suitable for food-related applications.
Why is certification under Regulation 1935/2004 EC important?
- Officially approved safety – Certification under European food regulations ensures that the material contains no harmful substances and is completely safe.
- Suitable for direct food contact – Ideal for making kitchen countertops, serving boards, bowls, trays, and other food-related products.
- Does not affect taste or smell – Once fully cured, it leaves no unwanted odors or substances that could alter food quality.
- Long-term mechanical and chemical resistance – The material is resistant to water, grease, cleaning agents, and everyday wear.
- Safe for professional and home use – A perfect choice for craftsmen, furniture makers, and DIY enthusiasts.
With LuminaCast 9 Ocean Flow, you can be confident that your epoxy products meet the highest safety standardsand can be safely used in direct contact with food.
What is LuminaCast?
- LuminaCast epoxy resin was developed with the aim of creating an unrivaled clear, UV-stabilized, and self-degassing system that's easy to use and covers the widest possible range of applications, particularly in the arts and crafts sector.
- Special attention was given to achieving the highest possible carbamate resistance in all formulations by using the latest raw materials and adding hydrophobic additives. Additionally, besides the most up-to-date UV absorbers and light stabilizers, this system employs only slightly yellowing base amines in the hardener and especially UV-resistant additives. LuminaCast is designed for every application in the decorative sector, be it basic coatings, trays, furniture, or large volume casting.
- With one resin and ten hardeners, you have maximum flexibility and can unleash your creative side!
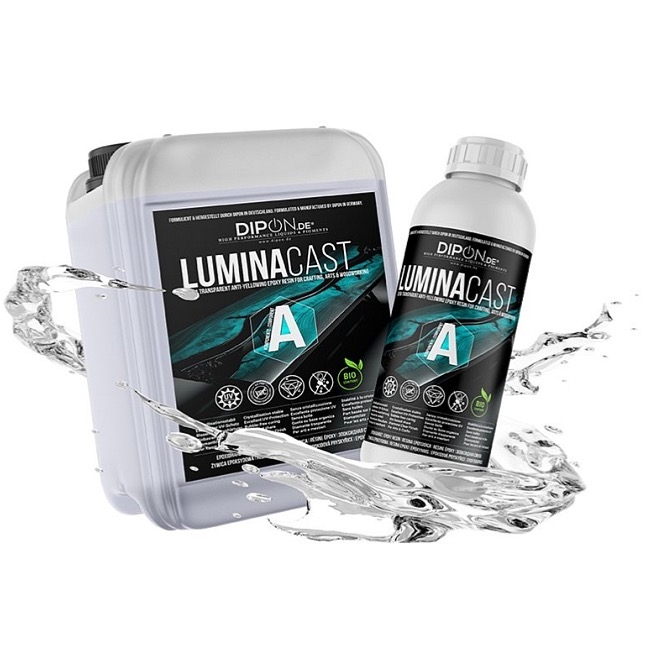
LuminaCast (A Component: 730 ± 50 mPa*s, 23°C) consists of ten hardeners and one epoxy
Type | *Dyn. Viscosity 23 °C (mPa*s) | **Proseccing time: 200g, 23 °C - 40 °C | Rec. Max. layer thickness | Purpose of use | UV protection |
---|---|---|---|---|---|
LuminaCast 1 Fast Set Primer | 120 ± 50 | cca 15 min | 0,1 mm - 7 mm | Pre-treatment & priming | Excellent |
LuminaCast 2 Coaster Cast | 290 ± 50 | cca 40 min | 0,1 mm - 15 mm | Highly transparent embeddings | Excellent |
LuminaCast 3 Crystal Flow | 140 ± 50 | cca 35 min | 0,1 mm - 10 mm | Laminations & Art | Excellent |
LuminaCast 4 Gem Flow | 890 ± 50 | cca 55 min | 0,1 mm - 20 mm | Art & Embeddings | Excellent |
LuminaCast 5 Radiant Flow | 1330 ± 50 | cca 60 min | 0,1 mm - 20 mm | Art & Embeddings | Excellent |
LuminaCast 6 Art Flow | 4100 ± 50 | cca 45 min | 0,1 mm - 20 mm | Art & Embeddings | Excellent |
LuminaCast 7 Design Flow | 5500 ± 50 | cca 50 min | 0,1 mm - 20 mm | Art & Embeddings | Excellent |
LuminaCast 8 Table Flow | 70 ± 50 | cca 180 min **500 grams, 9cm | 20 mm - 50 mm | Thick film potting | Excellent |
LuminaCast 9 Ocean Flow | 50 ± 50 | cca 240 min **500 grams, 9cm | 30 mm - 100 mm | Thick film potting | Excellent |
LuminaCast 10 Cell Flow | 2500 ± 50 | cca 50 min | 0,1 mm - 20 mm | Art & Embeddings | Excellent |
*Dynamic viscosity is measured at 23°C. A reduction in the material temperature is accompanied by a disproportionate increase in dyn. Viscosity. This is eminently important, especially when it comes to self-venting. Example. Viscosity Material temperature 23°C. 730 mPa*s, at 10°C Material temperature: approx. 10,000 mPa*s.
**The processing time is given for a mixture of 200 grams in a mixing cup (diameter 5 cm). Processing time = material temperature 23°C -> 40°C = doubling of the initial viscosity. The time to the max. exothermic temperature (tTMax) is usually twice the time of the prosecuting time.
- LuminaCast 1 Fast Set Primer - Low viscosity, pot life, approx. 15 min., can be poured over after 60 - 120 min., ideal as primer / sealer for porous substrates such as wood
- LuminaCast 2 Coaster Cast - Low viscosity, pot life approx. 40 min. ideal for decorative highly transparent embeddings and molds
- LuminaCast 3 Crystal Flow - Especially low viscosity, pot life approx. 35 min. ideal for decorative highly transparent embeddings and molds
- LuminaCast 4 Gem Flow Flow - Low viscosity, pot life approx. 55 min. e.g. for resin art with a higher viscosity, comparable to B20 JewelCast only more viscous
- LuminaCast 5 Radiant Flow - Medium viscosity, pot life approx. 60 min. a.o. like LuminaCast 4 GemFlow, somewhat slower and slower flow properties due to higher viscosity
- LuminaCast 6 Art Flow - High viscosity, pot life approx. 45 min. for painting techniques, resin art, worktops, sealers, similar to HoneyResin
- LuminaCast 7 Design Flow - High viscosity, pot life approx. 50 min. Special flow properties due to actuator, similar to LuminaCast 6 ArtFlow, perceived thinner
- LuminaCast 8 Table Flow - Low viscosity, pot life approx. 180 min. for large thick film castings e.g. for river tables, lamp production, larger castings in one casting
- LuminaCast 9 Ocean Flow - Low viscosity, pot life approx. 240 min. for very large thick film castings e.g. for river tables, lamp production
- LuminaCast 10 Cell Flow - Medium viscosity, pot life approx. 50 min. for cell effects, Petri Art, flower patterns, Resin Art, table tops, sealers etc.
Additional parameters
Category: | Individual Components of Epoxy Resin and Hardeners |
---|---|
EAN: | Choose variant |
? Temperature resistance: | 70 °C |
? Hardness: | 72 ShD |
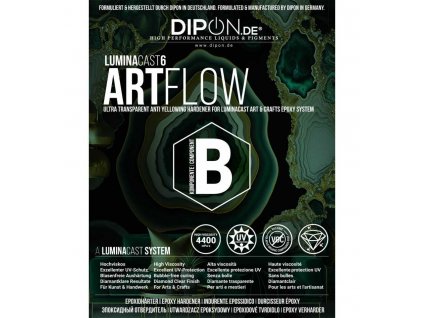
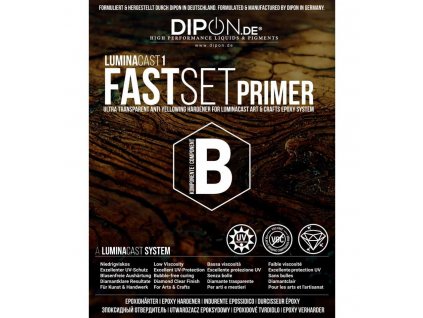
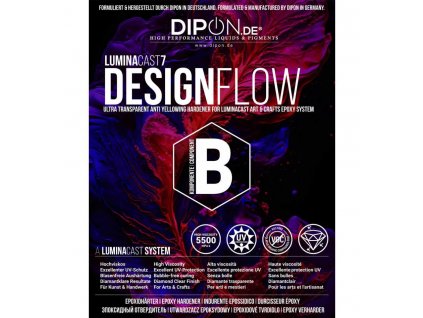

Hardener for Epoxyplast 3D resin designed for medium castings thickness 0.1 - 5 cm (at max 20 °C), cures from 15 °C, hardness 81 SHORE D, VOC 0 g/L, mixing ratio by weight 2:1,...


Epoxy resin (component A) for EPOXYPLAST B20 Jewel Cast, EPOXYPLAST B50 Deep Pour, EPOXYPLAST B100 Ultra Pour
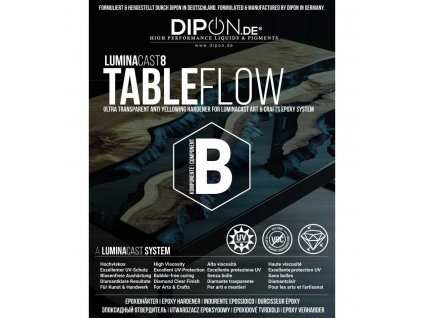

Tužidlo pro epoxidovou pryskyřici Epoxyplast 3D určené pro velké odlitky o síla až 10 cm (při max 20 °C), vytvrzuje již od 10 °C, tvrdost 77 SHORE D, VOC 0 g/L, mísící poměr...
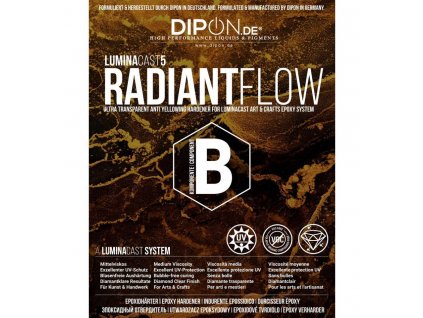
Be the first who will post an article to this item!
Be the first who will post an article to this item!
Manufacturing company : | DIPON.DE Removable Automotive Coatings GmbH & Co. |
---|---|
Address : | Ringofenstr. 39 I 44287, Dortmund, Deutschland |
E-mail : | info@dipon.de |